X-Press flex ASR 530
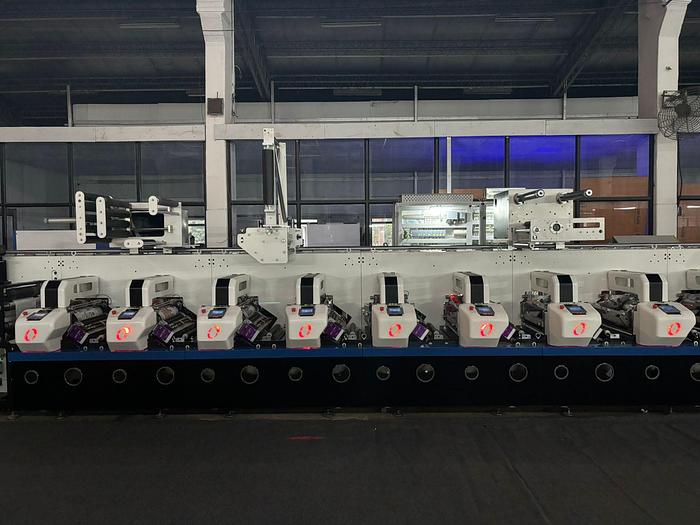
X-Press flex ASR 530
Location:Bologna, Italy
Description
The X-Press flex ASR 530 series is our 530 mm in-line Flexo press. This highly efficient and precise press is suited for printing on very thin films along with paper. This along with its width makes it an ideal replacement of many more traditional technologies and printing presses in the market today.
Focused on using innovation to provide customers with strong ROI’s this press is a must have in most modern converting and packaging businesses. This machine can be used for film labels, shrink sleeves, film pouches, mono cartons, paper labels etc.
The X-Press Flex 650 is the epitome of innovation, flexibility, and customer centric design.
What differentiates us:
- Orients proprietary X-gear design and gear box integration system allows for a PCD run out of only 2 microns leading to a much faster machine, very little noise, excellent registration, and higher print quality.
- Orients custom print unit design allows for faster job changes, better web handling, and more ease of use.
- Orient is also offering sleeve technology if required in the press.
- Orient uses higher grade of internal metallurgy than any of its competitors leading to a more robust and long lasting machine along with a more efficient one.
- A full backward integrated in house manufacturing unit and a full service and support staff across the country.
Item description:
ORIENT 530 ASR EXPRESS FLEXO MACHINE
- 8 color printing press 530 mm width
- Single servo motor at each station
- Motorized registration both lateral and circumferential
- Auto registration
- UV LED- 8 nos. (Orient Make)
- Cantilever unwind with closed loop tension with dancer andload cell
- Sliding trolley for loading roll at unwind
- Corona Treater
- Web aligner with splice table
- Web cleaner
- Infeed with closed loop tension.
- Ceramic Anilox 08 nos. (Make: Acme)
- 2 set of Print Cylinders
- Active static discharger in each unit
- Attachments on Rail: Relam- Delam - Turn bar - Cold Foil with differential shaft
- 1 die- cutting station with dial pressure indicator
- 1 set of magnetic cylinders
- 1no. Matrix rewinder
- Out feed with closed loop tension
- Rewind unit
- Organizer
- Print cylinder storage
Overview of Press Configurations
Press is designed with stress relieved and machined side frames connected by cross beam for proper alignment and rigidity to keep machine vibration free and with latest servo-based automation for the flawless operation of machinery.
1. Unwind Station (Servo Driven)
- Auto tension control system by dancer roll in a closed loop for precise tension control for the substrate throughout the process.
- Tension control is based on diameter calculations and feedback from the load cell.
- Pneumatic roll lifter for loading the substrate.
- Reel locking by cantilever 3" air expanding shafts.
- Unwinder driven by synchronous servo motor to keep proper tension for any kind of substrate web handling.
Splice Table:
- The splice table has been provided for the quick change over of substrate.
- Two pneumatic clamps have been provided to hold the front edge of the new reel and tail edge of the threaded substrate.
2. Corona Treater (Make: SOFTAL/ IEEC)
- Enhance the property of substrate to bond with ink and coating by blasting of corona over a substrate which increases its surface density.
- Cassette type with power of 2kW controlled through the remote switch.
3. Web Guide (Make: E+L)
- Edge positioning type with twin roll aligner and actuator
- Ultrasonic type sensor
- Auto and manual correction displacement ±14mm
- Manual positioning of the sensor
4. Web Cleaner (Make: Kelva)
- Web cleaning on both side with cleaning roll and active static bar discharger
- Remove the lint/ dust from the surface of the substrate before it enters the printing unit.
- Prevents ink from contamination.
- Prevents anilox cells from filling with contaminants.
5. In-feed
- Nip and pressure roller assembly with pneumatic cylinders at both end
- Isolates the tension between unwinder and first station
- Tension is maintained in closed loop by load cells mounted on both sides of the roller.
- Dirven by servo motor and drive
6. Printing Station
Printing Stations Designed for super quick change (Petal design-- concentric circles—No need for any adjustment after theplates is changed or just tiny adjustment after changing the different size of printing cylinders).
Printing unit comprises of:
- Ceramic anilox roller (included as per LPI at buyer’s choice)
- Ink tray with furnishing roller
- Doctor blade assembly
- Plate Cylinder (sizes at buyer’s choice)
- Hot air dryers
- UV LED dryers with for curing the ink
- Chill rollers on each unit
- Active statice discharger in each unit
- Automatic Registration control for quick setup and less wastage. Registration can be set manually as well through HMIprovided at each printing unit.
- Pre-registration for the quick setup of the job done with the help of sensor that senses the print cylinder position
- Re-pass option for re- printing with register (Optional)
- Variable printing with same repeat with range of ±4mm (Optional)
7. Delam/ Relam
- Delam/ Relam is on rail so that it can be moved accordingly to the no. of units depending upon colors to be printed on adhesive side.
- Delam separates the face stock from the liner to print on back side of label stock
- Relam re- laminates the face stock with liner.
8. Movable Turn Bar
- On rail to move according to the no. of units to be printed
- Both side printing is done by turning face stock or substrate
9. Cold foil
- Transfer the spot foil with the help of adhesive to the substrate for the embellishment.
- With independent servo motor driven unwind and rewind
- Nip roller addon at each station for proper transfer through a nip
- 3” differential shaft for foil saver for unwinding and rewind of foils
10. Peal and Seal
- Inline attachment given either over the rail with cross over unit for printing multilayer labels or coupon label.
- Or, in line with the printing unit with unwinder and rewinder over the rail to multilayer labels or coupon label.
- Web aligner on the top of unwinder for 2 layers.
11. Mid-feed unit (Optional) used mainly for controlling tension if the printing units are more than 10.
- Nip and pressure roller assembly with pneumatic cylinders at both end
- Isolates the tension between the infeed, print stations and out feed.
- Tension is maintained in closed loop by load cells mounted on both sides of the roller.
- Driven by servo motor and drive
12. Die Cutting Stations
- Choice 1-3 die cutting stations machine in to the machine
- 1st die cutting station with magnetic tooling is standard.2nd die cutting left idle and can be used later with deep through cutting and conveyor.
- Sperate servo motor drive for each die cutting station.
- High speed servo driven sheeting add on for beer labels.
- Servo controlled variable cutting length
13. Outfeed
- Nip and pressure roller assembly with pneumatic cylinders at both ends.
- Provides separate and independent tension zone between last printing and rewind unit
- Tension is maintained in closed loop by load cells mounted on both sides of the roller.
- Driven servo motor and drive
14. Matrix Rewind
- After the die cut the of the label stock, the waste face stock is rewound on the matrix rewind.
- Reel locking by 3” air expandable shaft.
- Separate servo motor and drive
- Open loop tension control by diameter calculation in program
15. Web Video Inspection (Make: E+L)
Standard Scope of supply:
- 55” Remote operated ultra-high-definition screen
- Digital color Video Camera
- Manual side traverse movement
- Sensor for line speed feedback
- Camera mounting frame installed between 1st and 2nd die cutting stations having alternate web paths to view front and reverse side of the substrate.
16. Rewind Station
- Auto tension control system by program-based calculation for precise tension control for the substrate throughout the process.
- Tension control is based on diameter calculations and feedback from the load cell.
- Pneumatic roll lifter for loading the substrate.
- Reel locking by cantilever 3" air expanding shafts.
- It is an active re-winder driven by synchronous servo motor to keep proper tension for any kind of substrate web handling.
- Inline slitting with rotary blade has been given before rewinder
- Active static discharge bar
17. Conveyor and stacker (Optional)
- Detachable conveyor unit servo motor for precise conveying and stacking of Sheets, IML and other full die cut labels
18. Plate mounter (Optional)
- For accurately mounting the plater over the plate cylinder consist of following components.
- Range of width of the cylinder that can be mounted: 350mm-600mm
- Lock for keep stationery the cylinder
- Holder of both sides adhesive tape.
- High - definition camera with zoom 2nos.
- The 650-line color high-definition camera can reach 70-times amplification
19. Central Automatic Lubricating System with pump and frequency control motor drive interlocked with the machine operation.
20. Electronics
- Main panel equipped with all digital ac drives, controls for auto registration, pre- registration, and other options etc.
- Complete pre- wiring up to machinery and operator console
- Touch screen for controls at each station.
- Emergency stops at each station along with main HMI.
- Separate 7” HMI for UV/ UV LED
- 10” HMI for Master control of the machine with all set parameters
- Web break through tension feedback
- Web end machine stops with internal calculation of dia.
- Panel AC
Specifications
Manufacturer | Orient |
Model | X-Press flex ASR 530 |
Condition | New |
Stock Number | 6258454 |
Max Web Width: | 530mm |
Max Printing Width: | 520mm |
Printing Repeat: | 177.8- 609.6mm |
Die – Cutting Repeat: | 304.8-609.6mm |
Max unwinding diameter: | 1050mm |
Max rewinding diameter: | 1050mm |
Max Matrix diameter: | 600mm |
Driving mode: | Full Servo (Single Servo each unit) |
Gear Pitch: | 3.175mm |
Max mechanical speed: | 180m/min (Actual Printing speed subjected to quality of materials, inks, and operator skill) |
Ink Curing: | UV LED, Hot Air Drying and IR Dryer |
Applicable ink: | UV LED Cured/ Eco friendly water-based ink/Solvent-based ink |
Substrate: | Paper/film/cardboard |
Substrate Thickness: | 12 Micron to 400 Micron |
Cliché: | 1.14mm |
Sticky Back: | 0.38mm |
Drive and Motors: | Rexroth Bosch |
Attachments: | Delam Relam (optional)/ Cold foil (standard)/ Peal and seal(optional)/Turnbar (optional) |
Tension Range: | 20-500 N |
Pneumatic: | 8 bar /20cfm non lubricated, dehumidified, and Filtered air |
Chill water: | 20-22 degree C |
Electrical Voltage: | 415V±10% |
Frequency: | 50 Hz (Standard) |
Registration: | Auto (both circumferential and lateral) |
Pre- Registration: | Yes |
Second pass: | Yes |