Automatic Laminator
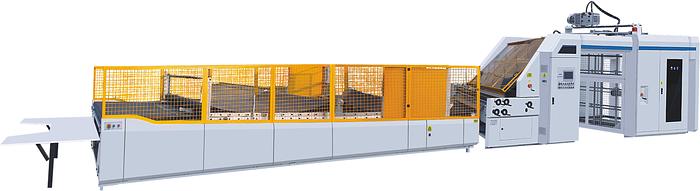
Automatic Laminator
Location:Bologna, Italy
Description
Automatic High Speed Flute Laminating Machine
Function:
The paper can be laminated with paperboard to increase the strength and thickness of the material or special effects. After the die-cutting, it can be used for packaging boxes, billboards and other purposes.
Structure:
- Upper Paper Feeder: It can send stacks of 120-800gsm paper from above.
- Bottom feed: It can send 0.5~10mm paperboard from below.
- Gluing mechanism: The glued water can be applied to the fed paper.
- Regulatory organization - Fits the two papers according to the set tolerances.
- Pressurizing Conveyor... Presses the attached paper and conveys it to the delivery section.
Principles:
The top paper is sent out by the upper paper feeder and sent to the start detector of the positioning mechanism for detection. Then the bottom paper is sent out; after the bottom paper is coated with glue on the glue wheel, the top paper and the bottom paper are respectively conveyed to the paper Synchronous detectors on both sides, after the detection, the controller calculates the error value of the paper and the bottom paper, and the servo compensation device on both sides of the paper compensates the paper to a predetermined position for splicing, and then pressurizes the conveying. The machine presses the paper and conveys it to the delivery machine to collect the finished product.
Applicable materials:
Paste paper --- 120 ~ 800g/m thin paper, cardboard.
Bottom paper---0.5~10m/m paperboard, single-sided cardboard, multi-layer corrugated paper, pearl board, honeycomb board, styrofoam board.
Glue - resin, etc., PH value between 6 ~ 8, can be applied to the glue.
Structural features:
- Adopting the world's leading transmission control system, only need to input paper size system auto-tuning.
- Computerized high-speed fitting, up to 150m/min.
- Chanliu-type air supply head, with four sets of forward nozzles and four sets of suction nozzles.
- Feed Block adopts low stack cardboard, which can fit the paper to the pallet, and can install track-assisted pre-stacker
- Use multiple sets of electric eyes to know the advance position of the bottom line, and make the servo motor on both sides of the face paper to independently rotate to compensate the upper and lower paper alignment, which is accurate and smooth.
- Full-function electronic control system, using human-machine interface and PLC program model display, can automatically detect operating conditions and work records.
- Automatic glue replenishment system can automatically compensate for lost glue and cooperate with glue recycling.
The transmission system
Use imported Servo motor electric controlling system, with Japan NITTA suction belt to make suction power inverter, and belt cleaned by water roller; Patented technology to ensure corrugate and cardboard goes out smoothly and simple operation.
Big suction system for bottom paper
If your products with cardboard, corrugated board, 3 or 5 layers, or twisted deformed corrugated paper. This system can feed them well.
Pre-stack part
Pre-pile system with preset function can be set as paper size through touch screen and oriented automatically to reduce set-up time efficiently.
Feeder system
Both paper lifting and feeding nozzle of high speed auto dedicated feedr can be freely adjusted to be adapted to both thin and thick paper. Together with Becker pump. Ensure top feeding paper run fast and smoothly.
Electrical system
Designed in the accordance with European CE requirement, ensure machine stability, high efficiency and low failure. Using man-machine interface and PLC combination, display all the information, such as warning, error detect, failures, and operating speed, etc on the screen at a glance.
Touch screen operational system
It adopts the centralised control of the touch screen, realises the man-machine dialogue with the high-resolution man-machine interface, and realises the real-time dynamic monitoring of operation and fault, making it more convenient to adjust and troubleshoot
Left-right positioning system
The right and left are accurately positioned with synchronous side stoppers, the bottom paper and top paper are precisely positioned, and the bottom paper and top paper are accurately positioned with left-right positioning devices.
Positioning system & glue roller
The use of multiple sets of photoelectric sensor at bottom sheets relative position, control top sheets on both sides of the servo motor to do independent compensation action, so that accurate positioning of top paper and the bottom paper.
Stainless steel roller, never rust, after narrowly grinding, guaranteed the minimum amount glue coated evenly. Down roller be cleaned by water roller.
Trasmission
Gates synchronical belt together with SKF bearing as main transmission is adopted to ensure stability. Both pressure rollers, dampening roller and glue value can be easily adjusted by handle with mechanical encoder.
Automatic lubrification system
Lubricate the bearing regularly to prolong the service life of the bearing
Leading EDGE feeding system (OPTIONAL)
This system is for option, more suitable for large size and thick bottom sheets.
Shaftless servo feeder(OPTIONAL)
This system is for option, more suitable for long size top sheets.
Top paper correction (OPTIONAL)
This system is for option, more suitable for long and narrow size top sheets.
Video monitoring (OPTIONAL)
This function can monitor machine running, operator need not walking around the machine frequently
Specifications
Manufacturer | BBS |
Model | 1200 / 1500 / 1700 / 1900 |
Condition | New |
Stock Number | 6258453 |
Max size: | 1200x1200mm / 1500x1500mm / 1700x1700mm / 1900x1900mm |
Min size: | 360x400mm / 360x380mm / 360x400mm / 500x500mm |
Top Paper: | 150 - 800 g |
Bottom paper: | 300 gsm-10 mm Corrugated board and cardboard |
Max speed: | 160 m/min |
Power: | 20 kw |
Stick accuracy: | ±1 mm |