Diecutter + Foil 1450T
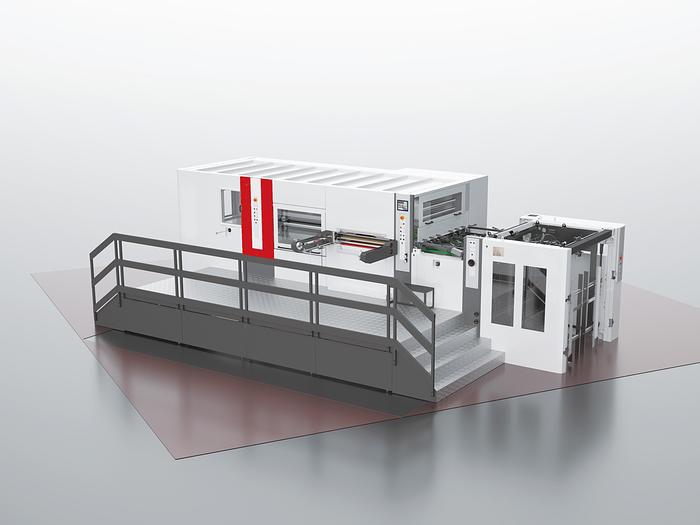
Diecutter + Foil 1450T
Location:Bologna, Italy
orCall +359 2 492 9330
Description
1. Feeding Unit
- Pile tray with handle allowing manual lateral correction of the pile during production
- German design automatic feeder with non-stop feeding offer by MABEG SHANGHAI MACHINERY-MMS
- Stream-wise feeding system with highest speed at 125 sheets per minute
- 4 suction cups each for lifting paper, five suction cups for moving paper
- Height and angle of suction heads are easily adjustable.
- 3 electronic safety devices preventing feeder pile from over ascending
- Micro-adjustment is available for transversal positioning of pile table
- Lateral blowing system enhances paper separation
- Precision double-sheet detector
- High pile design allows maximum pile height up to 1700mm
- The speed of the feeding belt is adjustable
- Easy changeover of pull and push side guides simply by turning a bolt without the need of removing and replacing complete side guide
- 2 front guides with micro-adjustment and the side guide is adjustable by wheel handle
- Side and front guides are with precision photocells, which can detect dark color and plastic sheet. The sensitivity is adjustable
- Single position engagement pneumatic operated mechanical clutch insures the first sheet after every re-start of machine is always fed to front lays for easy, timesaving and material saving make ready
- Photoelectric detector with automatic stop system on feeding table in case of paper jam
- Separate drive controls of main pile and auxiliary pile.
- PLC and electronic cam for timing control
2. Diecutting Unit
- Siemens main motor controlled by Schneider inverter control
- Micro-adjustment of cutting force by worm gear driven by motor and controlled by touch screen
- The pressure accuracy can be up to 0.01mm
- Crankshaft made of 40Cr steel
- Machine frames made of Q235-A Steel, upper and lower platens made of HT300 ductile iron with resin-coated sand with Meehanite Die Cast Iron Technology
- Accurate positioning of Cutting chase controlled by precision photocell sensors with automatic check lock device
- Cutting chase turnover device
- Overload protection device with torque limiter for the highest safety of operator and equipment
- 7 sets of gripper bars with grippers made of lightweight and durable aluminum alloy with ultra hard coat and anodized finish ensure accurate and consistent paper registration
- After long run test and delivered in pairs, main gripper, chain from Subaki, Japan
- High pressure index drive system for gripper bar positioning control
- Special designed gripper bar lock for compensation to insure accurate paper registration
- Pneumatic lock-up and release of cutting chase
- Cutting plate with aluminum base to protect the lifetime of the cutting plates and to reduce the noise when diecutting
- Centerline system for quick job changeover
3. Foil Stamping Unit
- 2 sets of individually controlled programmable foil pull rollers in Longitudinal direction driven by Panisonic servomotors
- 12 individually controlled heating zones , using intubation heating system ,with a tolerance within ±1°C
- Automatic foil feeding device for the ease of loading foil rolls
- 1 set of ductile iron honeycomb chase and locking device for dies
- Dwell time device is available for big area stamping
- Air blowing separation device is available
- waste foil will be collected Inside the machine automaticlly.
4. Delivery Unit
- Safety photoelectric devices preventing over-ascending and over-descending of delivery paper pile.
- Adjustable depressor brush helps unloading paper from grippers and piling up paper
- High pile design up to 1445mm
- Automatic auxiliary belt table available for non-stop delivery
- Feeder movement and speed control can be adjusted in the delivery unit.
5. Electric Parts, Operator Interface and Safety Detector
- The high speed Japanese industrial Omron PLC system
- Omron operator interface with touch screen
- Omron Electronic cam switch and encoder
- Electronic detectors, micro switched and photoelectric cells controlled by PLC on entire machine
6. Automatic Lubrication System
- Automatic oil pump and distribution system for entire machine with preset timer
- Lubrication oil distribution for gripper chains with individually controllable valve for each chain
7. Safety Devices and Quality Approval of Components
- All electronic and electrical parts are CE approved
- Overload protector for the protector and equipment
- Gripper chain clutch for the protection of gripper bars
- Emergency stop buttons on entire machine for quick and easy access
Specifications
Manufacturer | BBS |
Model | 1450T |
Condition | New |
Stock Number | 6258449 |
Maximum sheet size: | 1450×1150mm |
Minimum sheet size: | 650×450mm |
Maximum diecutting size: | 1430×1130mm |
Maximum Stamping Size: | 1430*1130mm |
Inside chase: | 1510×1215mm |
Maximum speed: | 5500 sheets/hour |
Maximum Stamping speed: | 4000 sheets/hour |
Maximum pressure: | 400 tons |
Sheet thickness: | 200g/m2 ~ 2000gsm/5mm B flute corrugated paper |
Heating Zone: | 12 Zones |
Programmable Feeding: | 2 Unwinds Shafts - Longitudinal Unwinder |
Total Weight: | 33Ton |
Total power: | 70kw |
Dimension (L × W × H): | 9560×5900×2800mm |
Delivery time: | About 6 months after receipt of down payment |