Orient JET L&P Series
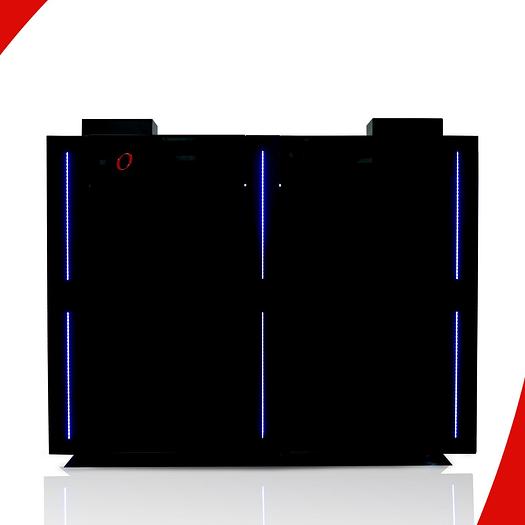
Orient JET L&P Series
Location:Bologna, Italy
Description
This machine is customizable in format and configuration. Each of our offerings is customised to our customer's specific needs.
- Orients proprietary Orient jet ink delivery system provides a more efficient use of ink leading to lower opex along with an ability to print on almost any substrate known to man.
- Orient has a proprietary in house software ensuring efficiency at every stage
- Fully backward integrated where everything is made in house so the press is fully customisable and due to our history we ensure excellent metallurgy and market leading web handling
- Full service and consumables team and our presses operating expense is extremely low and value for money.
- A full backward integrated in house manufacturing unit and a full service and support staff across the country.
Orient Jet L&P Series: High-Speed Inkjet Printing Press
Top-of-the-Line Performance
Offers high-speed inkjet printing capabilities
Available in 7 to 8 color options
Versatile Customisation
Multiple inline features
Tailored for diverse printing and packaging requirements
Ideal for Labels and Packaging
Specifically designed for label and packaging applications
Market-Leading ROI
Exceptional return on investment
Enhanced Productivity
Streamlined operations for superior efficiency
User-Friendly Design
Easy to operate, promoting seamless integration into workflows
Why Digital Solution in Label Printing?
- Rapid Production Turnaround: Emphasis on minimising production lead times to meet market demands.
- Brand Requirement for Personalised Communication: Necessity for tailored 1:1 communication strategies to enhance brand engagement.
- Declining Market Run Lengths: Observing a trend towards shorter print runs in the marketplace.
- Ongoing Demand for Short-Run Jobs: Continuous requests for short-run projects from end customers.
- Personalization Needs: Increasing demand for personalized printing solutions to cater to diverse consumer preferences.
- Compliance with Variable Data Printing (VDP) Requirements: Adherence to specifications for effective variable data printing.
- Track and Trace Capabilities: Implementation of systems for tracking and tracing printed products throughout the supply chain.
- Complementary Solutions to Flexo Printing: Digital printing serves as a supportive technology to meet emerging demands in the industry.
Overview of presso configuration
1. Unwind Station (Servo Driven)
- Auto tension control system by program-based calculation for precise tension control
- Tension range: 20-300N
- Pneumatic roll lifter for loading substrate
- Reel locking by 3 inch " air expanding cantilever shafts
- Active unwinder driven by servo motor
2. Splice Table
- Provision for quick substrate changeover
- Two pneumatic clamps to hold new reel and threaded substrate
3. Corona Treater
- Enhances substrate bonding with ink/coating by increasing surface density
- Cassette type with 2kW power, controlled remotely
4. Web Guide
- Edge positioning type with twin roll aligner and actuator
- Ultrasonic sensor
- Auto/manual correction displacement of ±14mm
- Manual sensor positioning
5. Web Cleaner
- Cleans both sides with cleaning roll and static discharger
- Removes lint/dust from substrate before printing
- Prevents ink contamination and anilox clogging
6. In-feed
- Nip and pressure roller assembly with pneumatic cylinders
- Isolates tension between unwinder and first station
- Tension range: 20-300N maintained by load cells
7. Pre-Printing Coating/Flexo Station
- Quick-change petal design for easy plate/cylinder
- changes
- Ceramic anilox roller (per chosen LPI)
- Ink tray with furnishing roller
- Doctor blade assembly
- Plate cylinder
8. Digital Printing Unit
- 600 x 600 dpi printheads from Kyocera Japan using Piezo DoD Technology
- LED Pinning after every Color Unit
- LED Curing
- Automatic printhead cleaning system
- Auto-Capping of printhead
- Air cooled pinning and curing
- Automatic variable ink drop size from 4 pl to 14 pl
9. Outfeed
- Nip and pressure roller with pneumatic cylinders
- Separate tension zone from last print to rewind
- Tension range: 20-350N by load cells
10. Post-Printing Coating/Flexo Station
- Quick-change petal design for easy plate/cylinder changes
- Ceramic anilox roller (per chosen LPI)
- Ink tray with furnishing roller
- Doctor blade assembly
- Plate cylinder (buyer's chosen sizes)
- LED Curing11. Rewind Station
- Auto tension by program calculation
- Tension range: 20-350N
- Pneumatic roll lifter
- 3" air expanding cantilever shaft reel locking
- Active servo rewinder
12. External RIP with Server
- RIP with Imposition and limited VDP capability from Arden
- Print Server from HP/Dell
- Workflow with Print Server and Color Management (Optional)
Specifications
Manufacturer | Orient JET |
Model | L&P Series |
Condition | New |
Stock Number | 6258416 |
Max Printing Width: | customisable |
Print Method: | UV Inkjet / Aqueous Inkjet (Optional) |
Color: | Wh+ C+M+Y+K (optional Orange, Violet, Special Color) |
Printing Resolution: | 600 X 600 dpi |
Max Roll Feeder / Winder Diameter: | 800 mm |
Substrate: | Paper/Polyester PVC/PP/PE/PETG/BOPP/Foil/Synthetic |
Substrate Handling Capability: | 12 to 240 microns |
Registration: | Auto (both circumferential and lateral) |
Printing Speed: | 60 mtr/min (speed may drop or increase depending upon the media) |
Compatible file formats: | PDF/ PDF-VT/PPML |
Operating conditions: | 24 Degrees, 46% Relative Humidity |
Dimension: | 5407 x 1788 x 2161 in mm |
Delivery time: | 3 months |